From concept to construction
We find out what actually goes into designing the bikes you know and love!
Words: Colin Levitch Photos: Mike Blewitt, Tim Bardsley-Smith, Matt Delorme
At its core, a bike is made up of two triangles, however the combination of angles, tube thickness, shape, and materials can be the difference between a frame that rides like a race rocket or a beach cruiser.
Beneath the marketing jargon, and the Daft Punk theory of innovation (every bike is faster, stronger, lighter, better), thousands of hours of engineering goes into to creating a bike where the front wheel doesn’t drift on a steep climb, or a long travel sled that can monster through even the rowdiest of rock gardens.
The lifecycle of any given frame is about three years and from the day a new bike is launched the design teams are already hard at work testing and tinkering on the next model to help pros and everyday joes alike.
We’ve highlighted two completely different bikes, the brand new Norco Revolver and the Nukeproof Mega 275c, to gain some insights into what went into taking a concept through to construction.
Unleashing the Norco Revolver
The Revolver is Canadian brand Norco’s purebred XC racer which has guided riders onto podiums in the Swiss Epic, Crocodile Trophy and Commonwealth Games. With a growing pedigree of results, when Norco started looking at how to make improvements, the design team had to take into account the increasing difficulty of modern cross-country race courses.
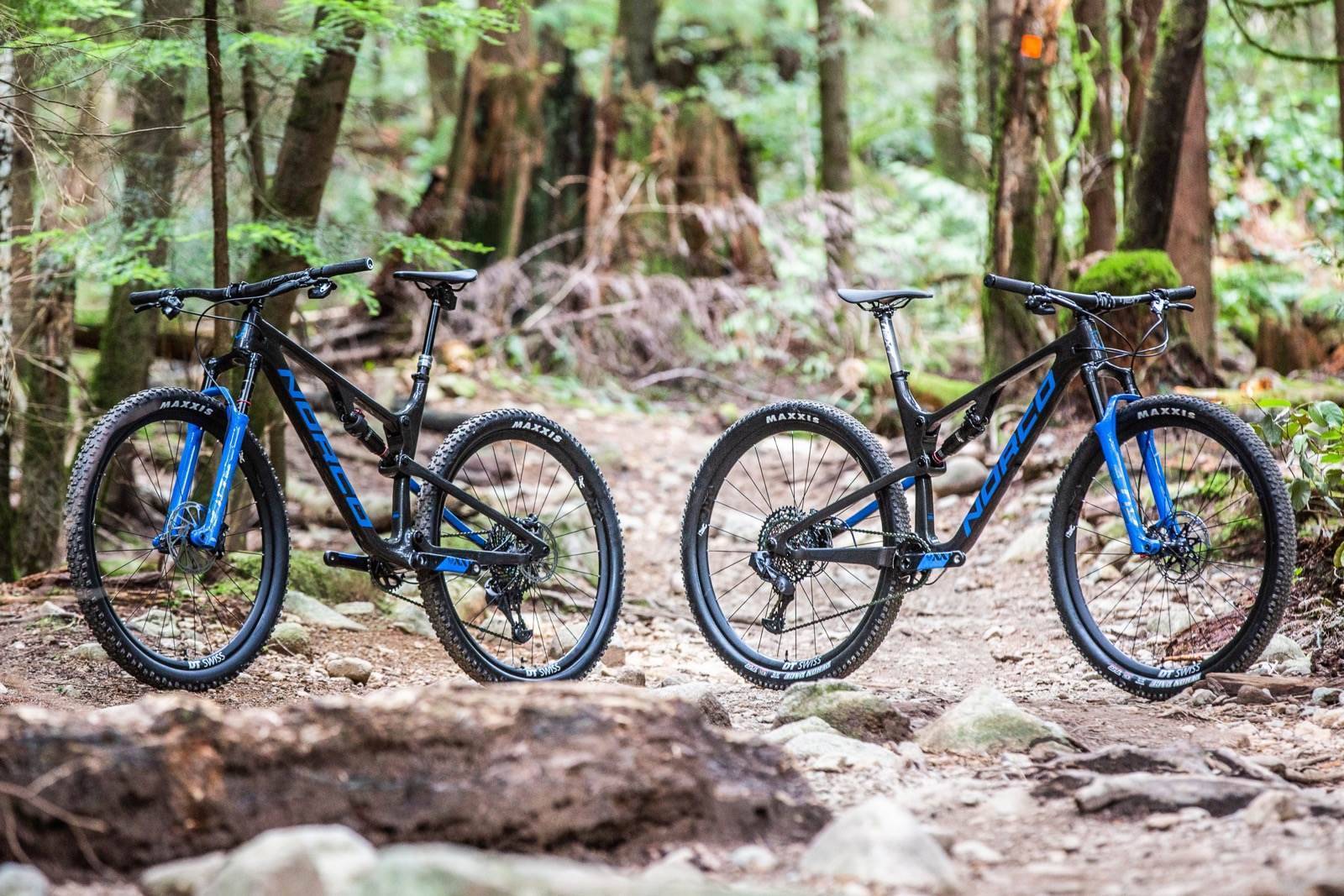
“The first question we have to ask is, is the current bike sufficient or is it getting pushed to the limit of what they (our riders) can do,” says Paul Burnett, Norco’s Product Manager. “If you follow cross-country, the courses are getting harder and there is more gnarly stuff. You need to make these changes to classic cross-country race geometry to make it less fatiguing and give riders more confidence on the downhills.”
The design team at Norco noted that as XC courses have evolved, and to cope the brand’s factory team riders were having to maintain a forward pedaling position on the uphill, and then were off the back of the bike in total survival mode on the descents. So when approaching the new Revolver the goal was to move their center of gravity forward and down.
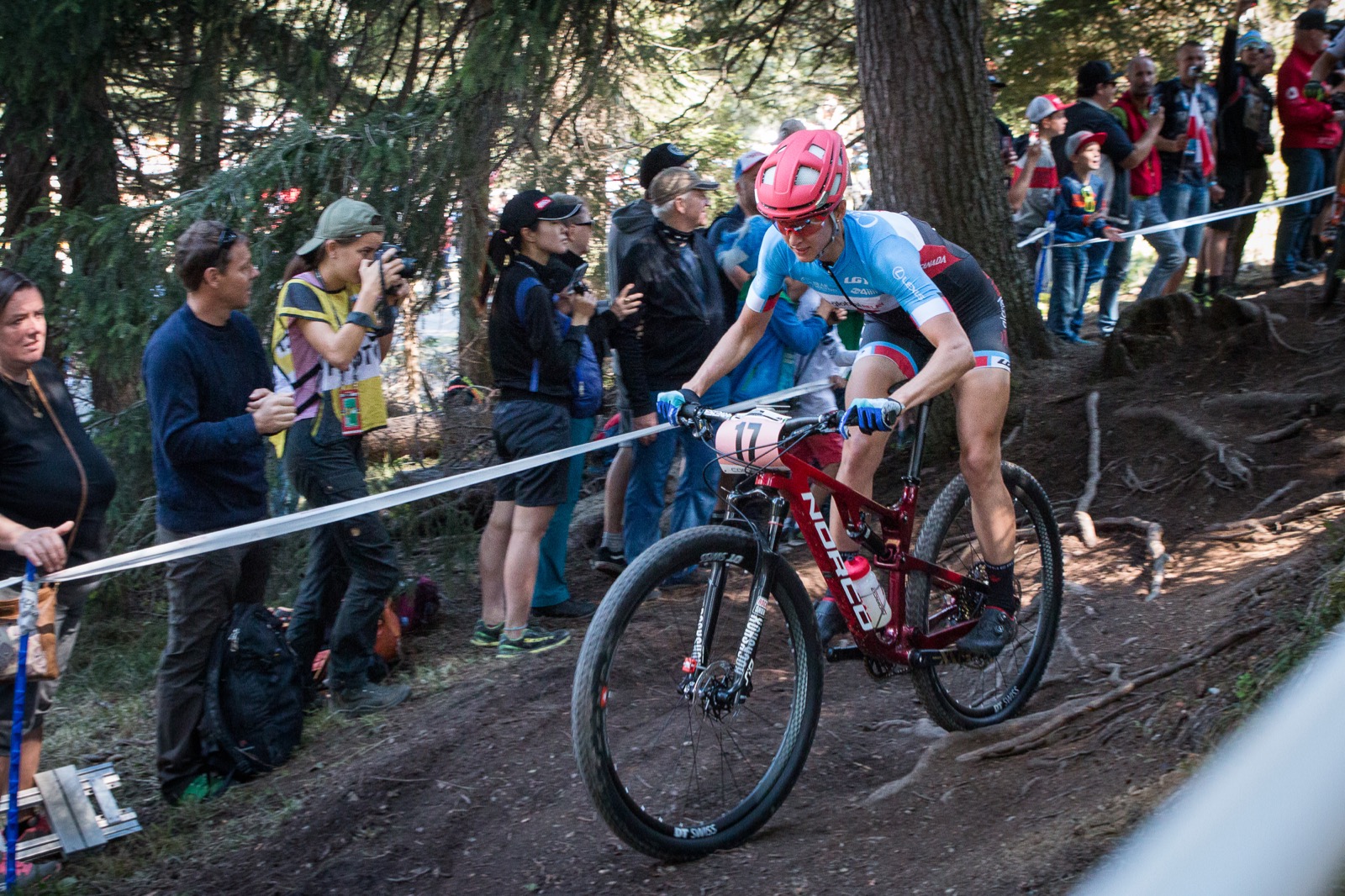
“The purpose behind (updating) the Revolver was to stabilise the rider’s weight distribution over the course of the race. So you would see these riders where continuously having to shift their weight over the front on longer ascents as soon as there was a decent grade or technical terrain to keep the front end from floating and give traction to the rear wheel—they were in a constant state of recovery,” says Arthur Gaillot, who looks after the suspension base tunes for Norco.
“We started off with a head angle, stack height, stem length that we felt worked really well together, and the bike is designed around a 60mm stem which is aggressively short for a traditional XC bike. Because the stem length is short we could lengthen the top tube and the reach of the bike up to the stem. Then we could look at the seat angle so that the rider is moved more into that more forward position…so the seat to bar distance is still comfortable,” says Norco Engineering Manager David Cox.
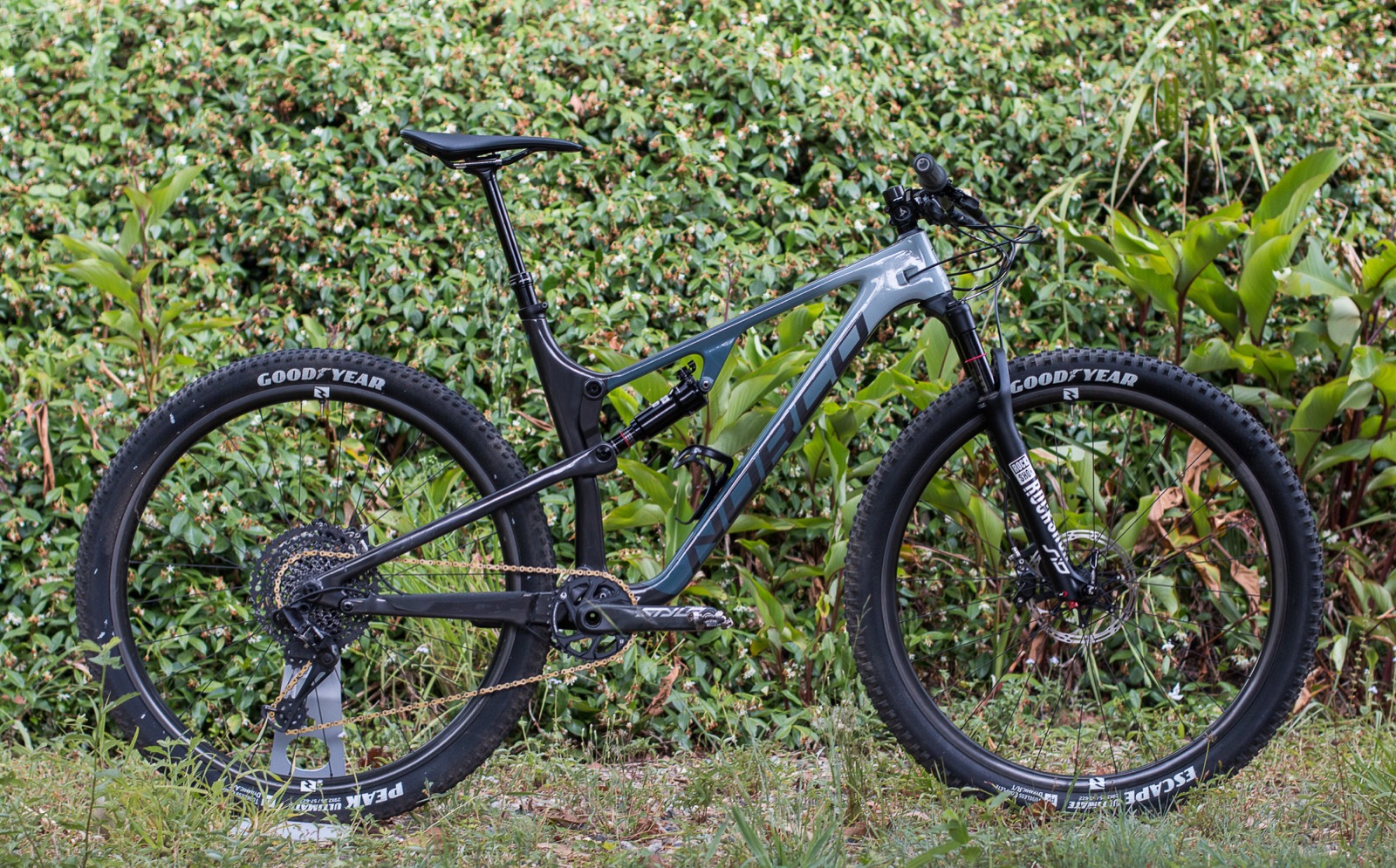
Haley Smith, one of Norco’s Factory Team riders got her hands on the new Revolver in the middle of the racing season, and it only took one ride ahead of a Canada Cup race before the Ontario native decided to make the swap. Five days later she rode the new frame to a career best World Cup result at Mount Sainte Anne.
“My first thought was that the bike looked more relaxed, like the old Revolver’s cooler younger sibling. Once I rode the bike, I realised that the relaxed geometry actually makes the bike faster, while at the same time making it feel reliable and stable,” she says.
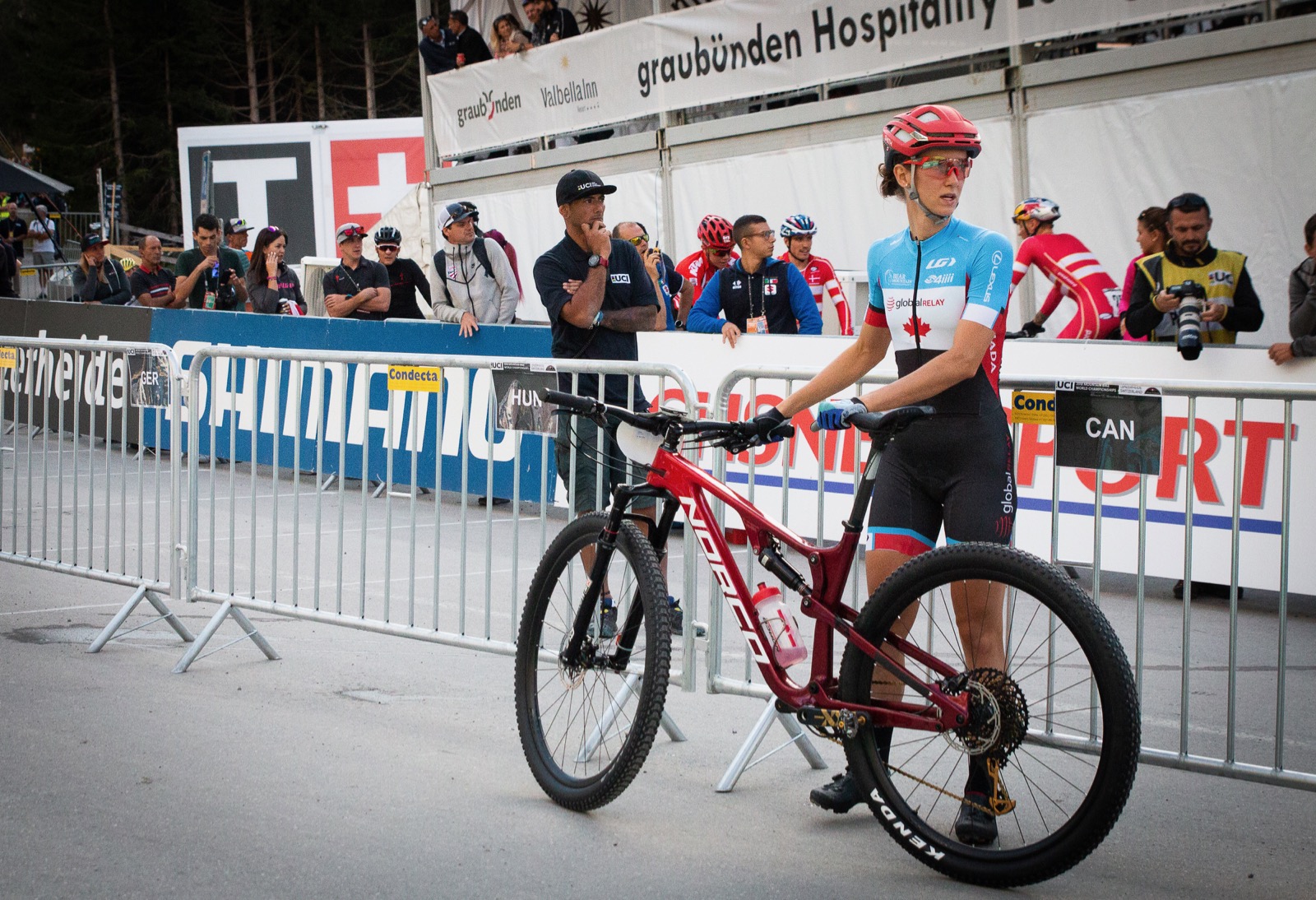
“I used to ram my saddle all the way forward in order to get the pedalling position I wanted, which ended up putting my centre of mass really far in front off the rear axle. With the updated geometry, I can run my seat more in the middle for optimal pedalling position, while allowing me to keep the rear end of the bike more nimble,” she continued.
There is no question the descents are playing a bigger role in the final results, but cross-country races are still won on the climbs. So, many World Cup XC riders, including Norco’s Factory Team, were slamming saddle rails and swapping for long negative degree stems to achieve the most efficient climbing position. This in itself answered Burnett’s question, the Revolver’s geometry was no longer sufficient, so Norco sought to solve the changes riders were making with components with the frame itself.
“When you look at someone like Jaroslav Kulharvy’s bike, it looks insane and nobody can actually ride that except for him—nobody really should it just looks like you’re in a horrible position. We thought we could do better,” Burnett says.
Cox continues, “That bike is a really good example, you can look at what he’s done to the bike to enable the bike to perform the way that it needs to, so we worked with riders on our XC team to get feedback and understanding as to why they were altering their position on the bike, what their intended outcome was and how we could actually fix that.”
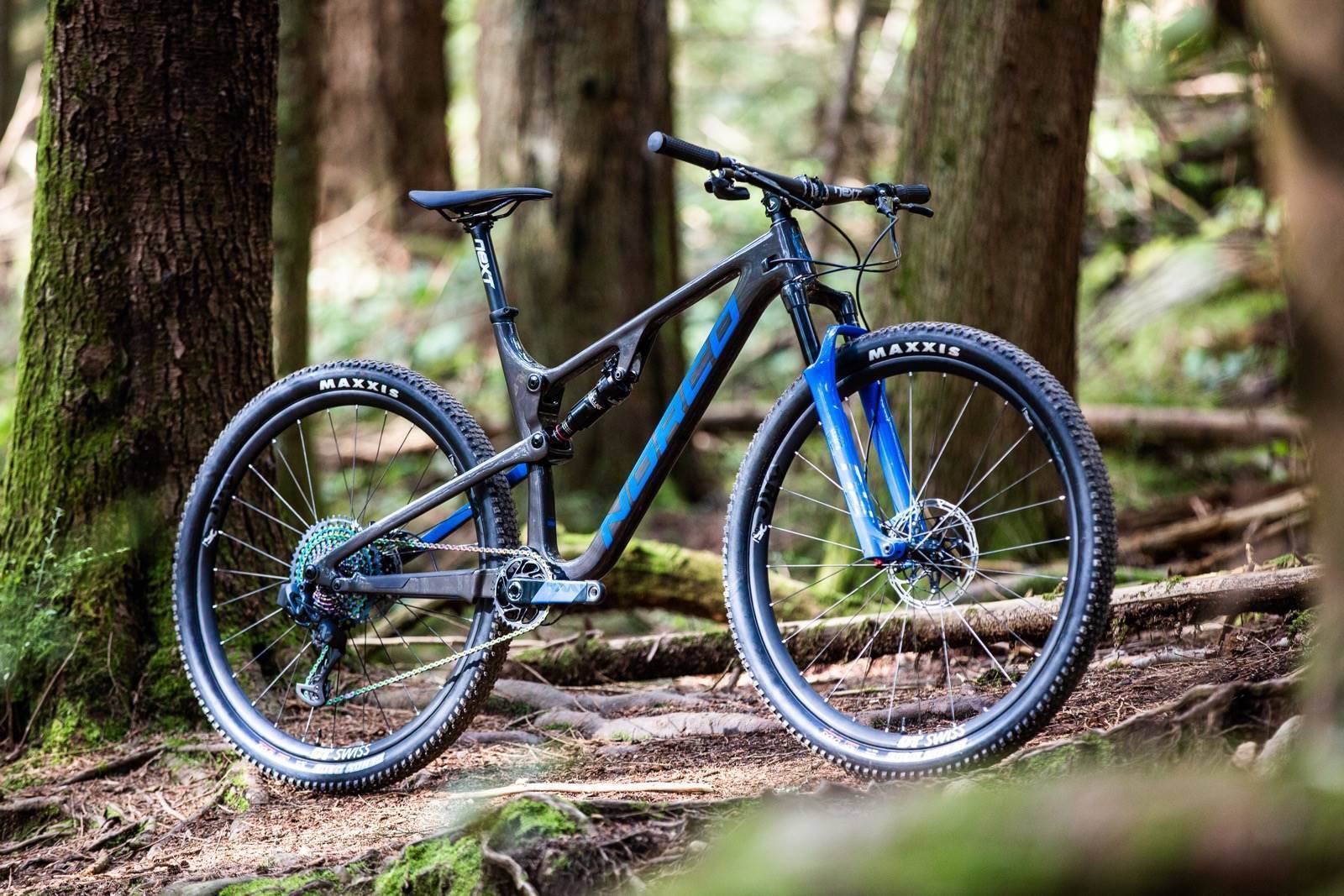
Once they had this feedback back from the riders, the tinkering began. Burnett’s starting point was to jump on an XL of the old Revolver (he usually rides a size large), smash the saddle forward and install a stumpy short stem. This gave him a rough starting point for the geometry they were trying to achieve with the new frame, namely the changes to the reach and the weight shift they were looking for, but, that was only the beginning.
With the cost of cutting carbon moulds, once the geometry and suspension parameters are finalised, the brand utilises 3D printing to make sure they won’t be making any expensive mistakes when the designs are sent to the manufacturer.
“We get full 1:1 rapid prototypes 3D printed, I think we actually use the biggest printer in Canada to actually 3D print, and I’m pretty sure we can actually do a hardtail in one piece. So we print the front triangle and the stays and then we will put bearings and hardware into the bikes and build them up as complete bikes,” Cox explains.
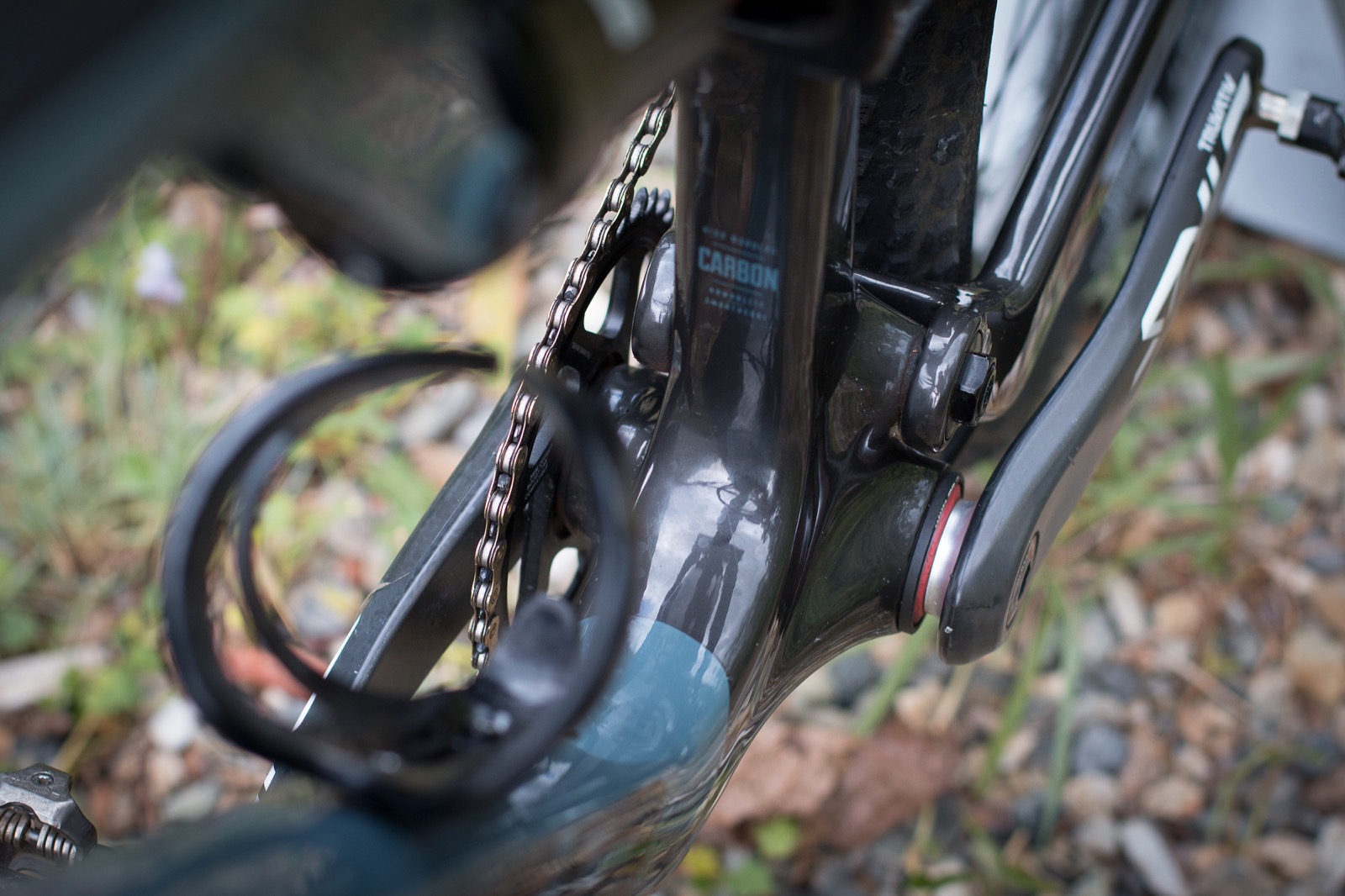
“By the time we are done with that the prototypes are destroyed cause we’ve drilled holes in them and the graphics team have gone out and put stickers all over them so they are kind of multi purpose. But, that is the most useful way to figure out those fine details because the last thing you want to do is have carbon moulds made and find out that we’ve got cable routing problems.”
After months of testing, the final result is actually two versions of the new Revolver, with the new bike coming in a 100mm travel version and a 120mm version as well—they utilise the same frame, just slightly different components. The 100mm version uses a 37.5mm shock stroke on the 190mm body, while the 120mm version uses a 45mm stroke. However both see a slacker frame, with more reach and a lower headtube, allowing riders like Smith to achieve the position they were looking for and run the stock 60mm stem.
Creating the Nukeproof Mega 275c
Ridden to two consecutive Enduro World Series overall all wins, Nukeproof’s first ever carbon frame, the Mega 275c, started life as a side project designed to conquer the Megavalanche.
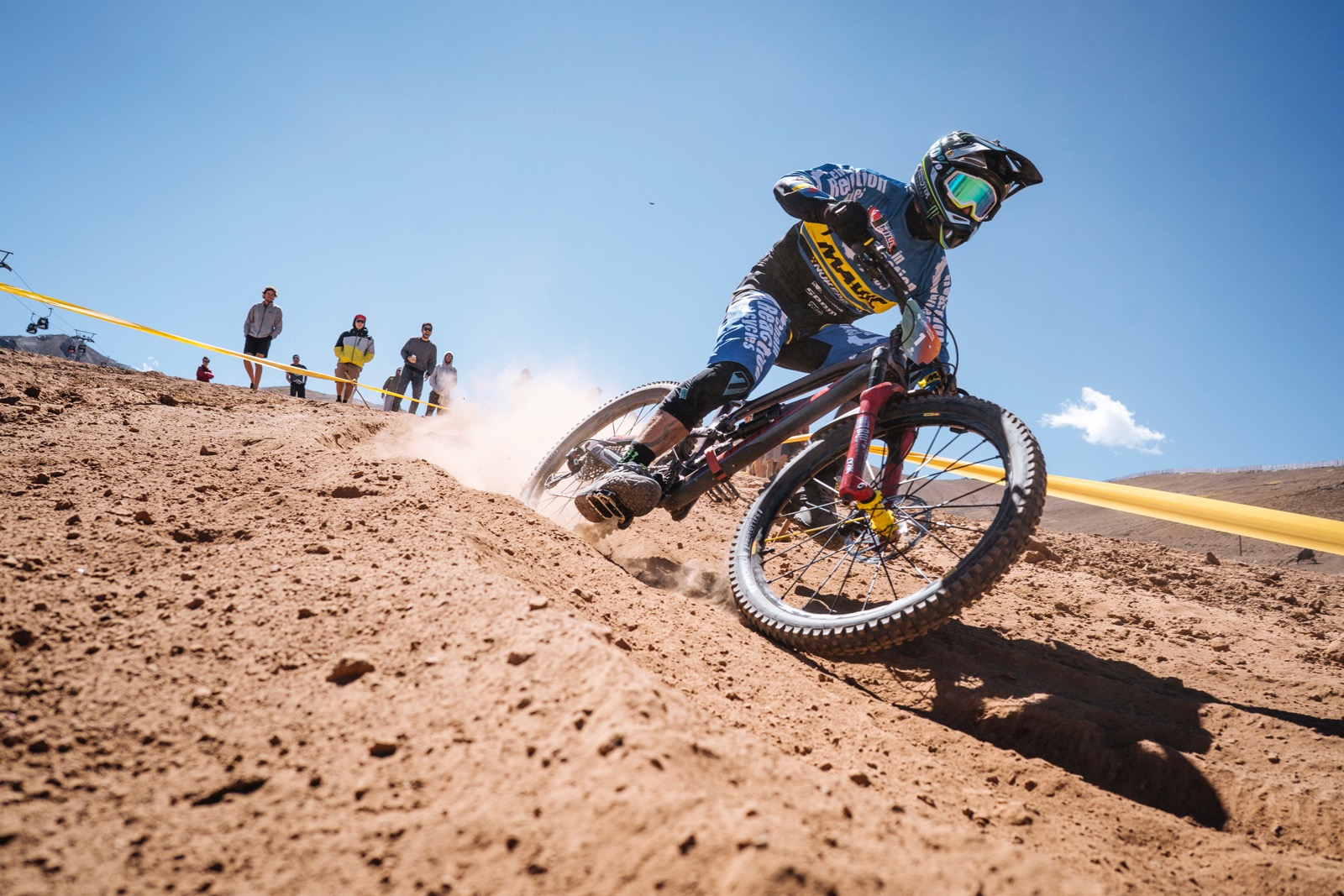
“The original concept of the Mega came at a time where we were discussing with CRC team manager Nigel Page the potential to sponsor the race team with frames as well as components. The only issue was we didn’t have any frames,” said Nukeproof Marketing Manager Rob Sherratt. “In the background Dale McMullan (Engineer) and Michael Cowan (Owner) had been developing a bike to take on the Megavalanche. They had reached the limit of what they could modify on their trail bikes and developing their own frame from scratch to blend the best of their downhill and trail bikes (all mountain/ Enduro wasn’t really a category in 2008).”
While Nukeproof bikes have come quite a long way over the years from the industrial looking tanks from the brand’s infancy, the Mega, as with all of Nukeproof’s bikes started with a pencil and pad of paper.
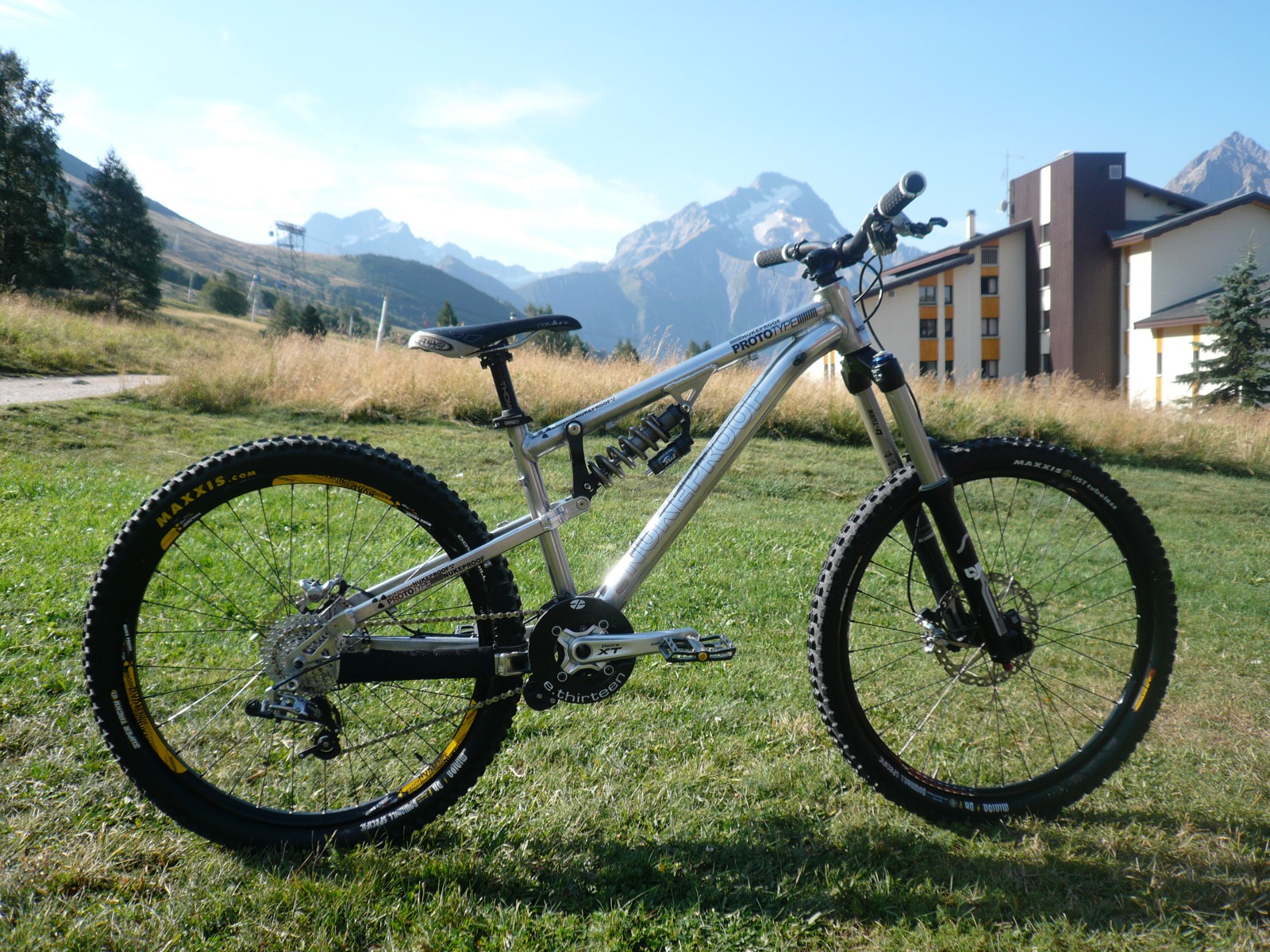
“The overall packaging of the bike will always come from the linkage points, which Dale designs to give the characteristics he was looking for from the bike. The sketching of the general look of the concept is all done in house by our graphic designer Enrique Repellos,” says Sherratt. “This is generally still the process for all new products to this day. Dale will design/engineer the bike and the linkage with Enrique on the sketch pads. However, we now have a 3D modeling department to help bring these to life, test and engineer the bikes prior to production”
“The frame design starts around 3D linkage/suspension points, then wheels, geo, components, this way we can ensure things will fit and the first prototype will work, we also do a lot of FEA testing to ensure the design will be strong enough to pass ISO and ride testing, this saves a lot of time in the long run,” he continues.
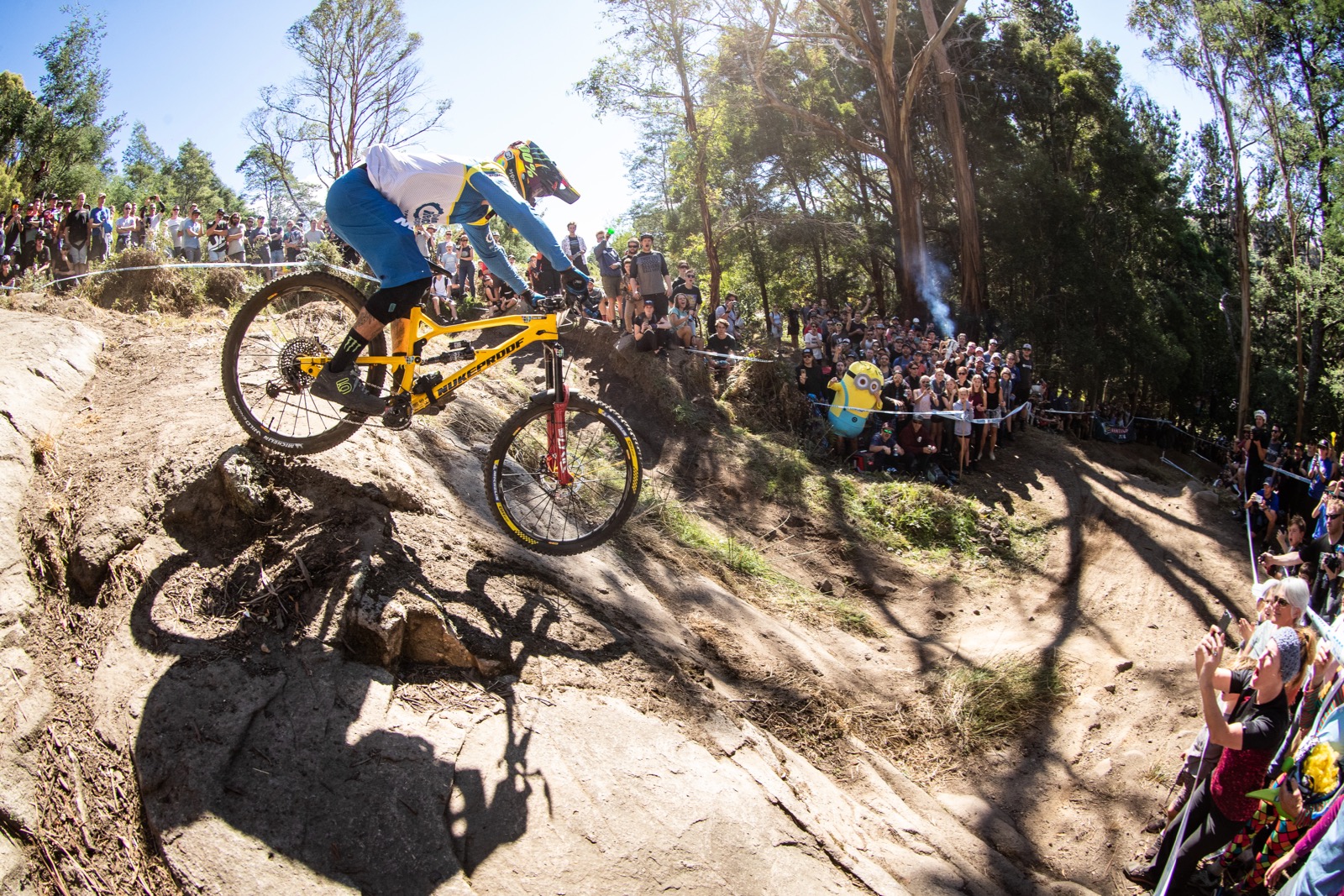
With Nukeproof being a smaller brand, they run a tight ship and involve its sponsored athletes from the outset.
Sam Hill’s Mega input
How much does Nukeproof involve you in the design process?
“They actually talk to the team and us riders a lot for any suggestions on what we want the bike to be like or the characteristics we would like to see in future bikes. They take our feedback onboard so that’s awesome.”
From the 2016 model, what changes did you want to make to the frame? What worked from the 2016 frame and what didn’t?
“I thought the frame was actually already pretty good but we changed the head angle to suit a 170mm fork from the previous 160mm. They incorporated the metric shock which increased the rear travel slightly and also made the rear end work a lot more freely on the smaller bumps. They also worked hard getting the carbon model just right.”
When you first got your hands on the new 2018 bike what was your first impression? As you spent more time with it what differences became apparent to you in terms of ride characteristics?
“It was obvious straight away how much plusher the suspension was, it just plows through anything. The bike blows me away being a trail bike and how well it handles any terrain you throw it down. The Mega 275c is the Nukeproof’s first carbon frame, I didn’t really push for it at all, I was really happy with how my aluminium bike handled and rode. I was a little sceptical as a previous experience with another company I didn’t gel with the carbon bike they built. When Nukeproof had prototypes of the 2018 frames they sent me an alloy bike and a carbon bike to ride and test and I preferred how the aluminium bike handled. I gave my feedback to Nukeproof and after a couple of different versions of the carbon bike they got it handling awesome and ever since then I’ve been racing it. I think it’s easy to over build carbon fames so it was awesome to see and help the guys to keep trying to find the perfect balance and feeling in the bike.”
Though it may have started analogue, the latest Mega launched in October of last year is anything but. According the Sherratt, the brand felt they had a pretty good jumping off point with the 2016 bike; there weren’t too many geometry changes bar some scaling between the larger sizes. Many of the improvements Nukeproof was looking to make came through implementing new technology like Metric shocks and bosst rear spacing. The biggest however was jumping headfirst into carbon fiber.
“This was our first carbon bike with the Mega 275c…we had to ensure that the 275c had the performance benefits over its alloy counterpart and was not just to be an aesthetic project,” Sherratt said. “Obviously, it needed to be lighter, but also comfortable to ride, not too harsh without loss in front triangle stiffness. We looked to offer even better performance downhill and also improved pedalling performance over rough ground.”
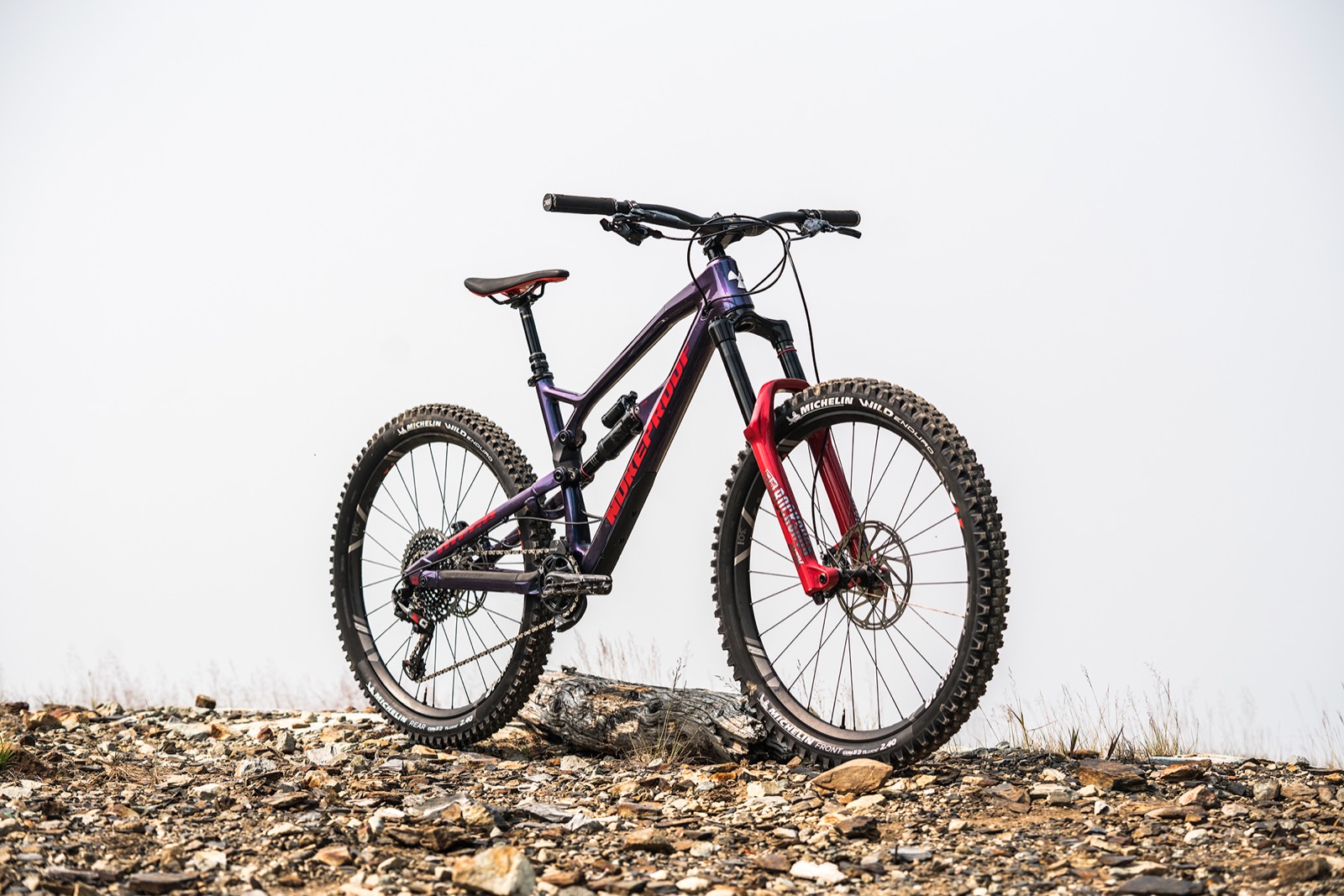
Being that the Mega 275c is Sam Hill’s bike of choice, it’s no short order for Nukeproof to deliver the best possible platform for the EWS.
“It’s a balance between strength, weight and cost. Carbon is generally less stiff than alloy so we need bigger sections just to match the strength and stiffness. If desired, you can achieve radical shapes but generally it’s at the cost of weight and extra time to hand finishing the carbon where the carbon has difficulty filling the corners of the mold,” Sherratt said. “These can be weak spots with excessive resin or air pockets that may need filling. At the end of the day, the bikes are performance frames so how we achieve the maximum strength/weight balance is the main factor before aesthetics.”
“Alloy is more cost effective initially, but your design needs to consider if the tubes are to be hydro formed or mechanical formed, this will have a big impact on tube cost and tooling cost.”
Carbon of course brings a whole pandora’s box of variables, but the other area where Nukeproof sought improve the anti-squat performance.
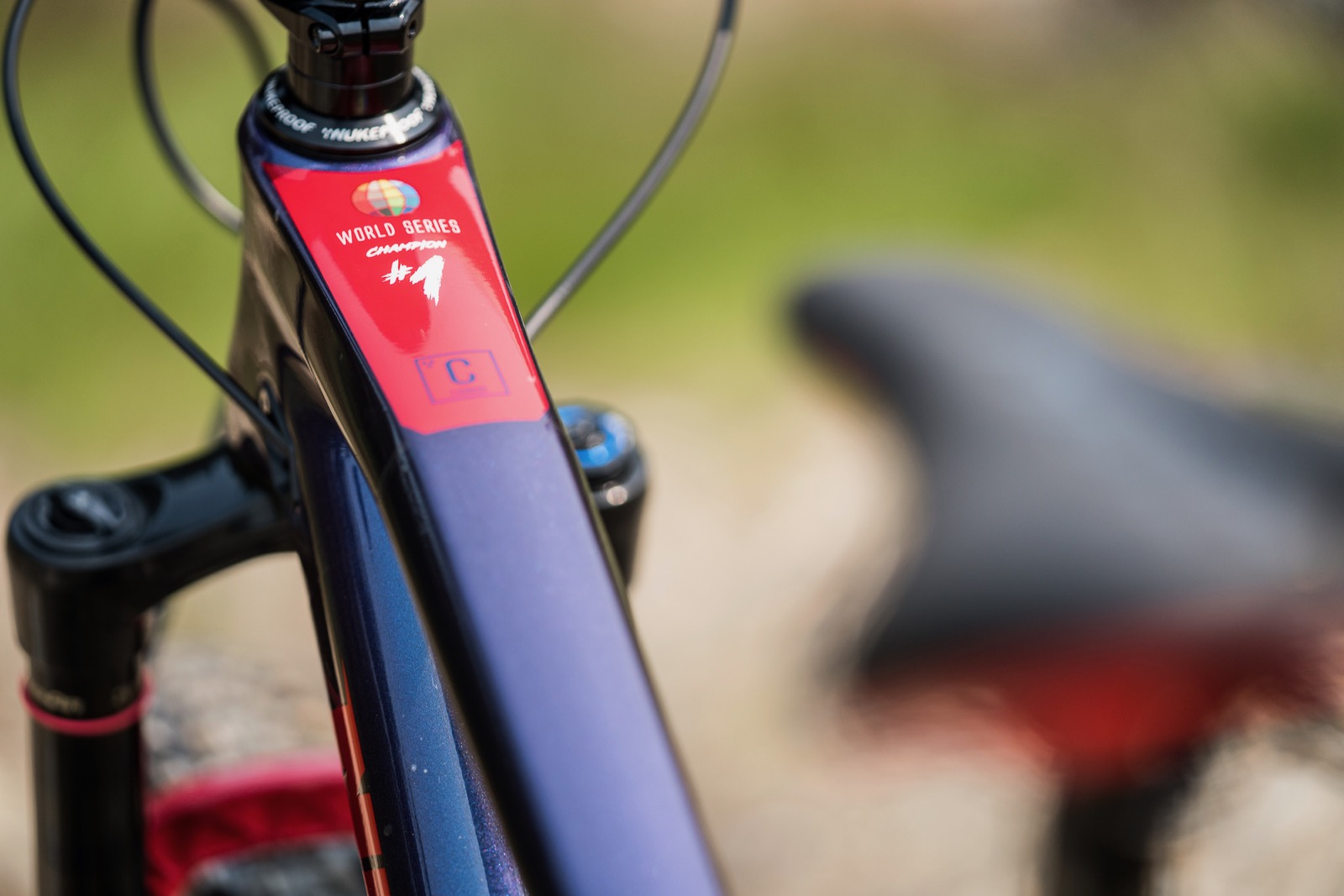
“We had high levels of anti-squat (very trendy at the time) between 117% and 132% depending on gearing,” says McMullan. “For the current Mega we wanted to un-restrict the suspension from the chain by dropping the anti squat figures, we were also able to control the anti-squat % for climbing and descending.
“(On) the old bikes, anti-squat increased when descending in high gears and reduced for climbing in lower gears (very common), this didn’t make sense so with the new Horst link design we were able to flip this, so now the anti-squat drops for descending and increases for climbing,” he continued.
Like with the team at Norco, just because the latest Mega 275c was just launched late last year Nukeproof’s engineers are already hard at work looking at the next version. Sherratt and his team didn’t give too much away about their plans for the new bike, they did say they are examining the boundaries of reach, and like Burnett have been riding one frame size up to see what’s possible—McMullan says he has to cut the seat tube to accommodate his short legs.
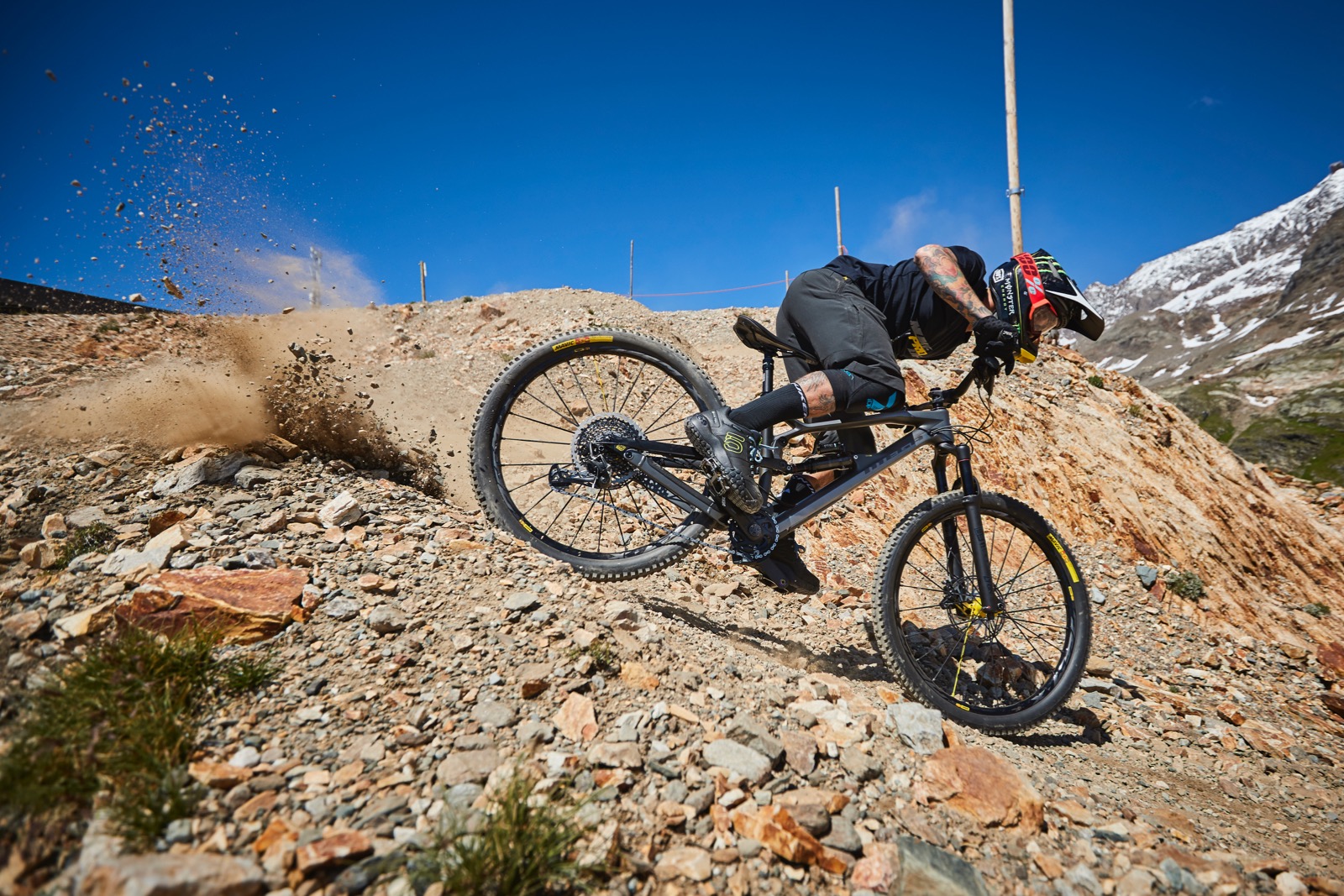